Blowing Equipment
PET (Polyethylene Terephthalate) blowing equipment is machinery used in the manufacturing process of creating PET plastic containers through a process called blow molding. Blow molding is a manufacturing technique used to produce hollow objects, such as bottles, containers, and other plastic products.
​
PET is a common material used for creating plastic bottles due to its clarity, strength, and ability to be easily molded into various shapes. The PET blowing equipment specifically refers to the machinery used to transform preforms (small, test-tube-like plastic forms) into final PET containers.
​
PET-blowing equipment comes in various sizes and configurations, ranging from small machines suitable for producing a few hundred bottles per hour to large industrial systems capable of producing thousands of bottles per hour. This equipment is an essential component of the plastic bottle manufacturing industry and plays a crucial role in producing a wide range of consumer products, including water bottles, soda bottles, food containers, and more.​

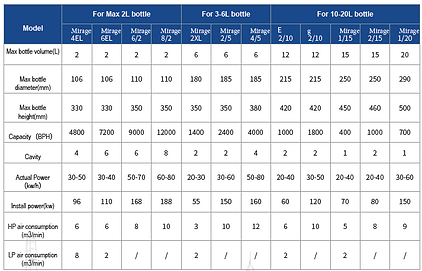
Mirage 4th Generation
-
All servo-electric motor, no need for a low-pressure air compressor
-
Energy savings: 4-cavity operating power 20kw, 6-cavity operating power 25kw, 8-cavity operating power 32kw
-
Designed for an easy and fast mold change
-
Bottle blocking monitoring: Designed to detect blocked bottles in the air duct, start the automatic bottle-dropping device, and protects the blow molding machine.
-
Pressure monitoring: Designed to detect low blowing temperature limit, automatically stops the preform loading and reduces the amount of wasted preforms. and start the bottle-dropping device at the same time, so any unqualified bottles will not enter the filling machine
-
Temperature monitoring: Designed to detect the temperature of the performs, if it is too low, it automatically stops feeding the preforms to reduce the waste of the preforms
-
Empty Blank Detection: When there is no preform for a long period of time, the oven will automatically enter a standby state, reducing energy consumption and prolonging the service life of the oven.
-
​Constant Temperature Heating: The light box is controlled by 5 variable frequency fans to ensure that the hot air stays below the support ring in order to protect the bottle mouth, and at the same time circulate the air volume to ensure the constant temperature of the oven and the consistent process.
-
Precise Cam Link Control of Molds: This process greatly simplifies the structure, and the action completed in one go, improving accuracy and output while reducing both failure points and maintenance points. Unlike traditional mold opening and closing, mold clamping, sealing, etc. which are independently controlled by air cylinder photoelectric.


Mirage 3rd Generation
-
All servo-electric motor, no need for a low-pressure air compressor
-
Energy savings: 4-cavity operating power 20kw, 6-cavity operating power 25kw, 8-cavity operating power 32kw
-
Designed for an easy and fast mold change
-
Bottle blocking monitoring: Designed to detect blocked bottles in the air duct, start the automatic bottle-dropping device, and protects the blow molding machine.
-
Pressure monitoring: Designed to detect low blowing temperature limit, automatically stops the preform loading and reduces the amount of wasted preforms. and start the bottle-dropping device at the same time, so any unqualified bottles will not enter the filling machine
-
Temperature monitoring: Designed to detect the temperature of the performs, if it is too low, it automatically stops feeding the preforms to reduce the waste of the preforms
-
Empty Blank Detection: When there is no preform for a long period of time, the oven will automatically enter a standby state, reducing energy consumption and prolonging the service life of the oven.
-
​Constant Temperature Heating: The light box is controlled by 5 variable frequency fans to ensure that the hot air stays below the support ring in order to protect the bottle mouth, and at the same time circulate the air volume to ensure the constant temperature of the oven and the consistent process.
-
Precise Cam Link Control of Molds: This process greatly simplifies the structure, and the action completed in one go, improving accuracy and output while reducing both failure points and maintenance points. Unlike traditional mold opening and closing, mold clamping, sealing, etc. which are independently controlled by air cylinder photoelectric.
Mirage GB (Gallon Blower)



PET (Polyethylene Terephthalate) blowing equipment is machinery used in the manufacturing process of creating PET plastic containers through a process called blow molding. Blow molding is a manufacturing technique used to produce hollow objects, such as bottles, containers, and other plastic products.
​
PET is a common material used for creating plastic bottles due to its clarity, strength, and ability to be easily molded into various shapes. The PET blowing equipment specifically refers to the machinery used to transform preforms (small, test-tube-like plastic forms) into final PET containers.
​
PET-blowing equipment comes in various sizes and configurations, ranging from small machines suitable for producing a few hundred bottles per hour to large industrial systems capable of producing thousands of bottles per hour. This equipment is an essential component of the plastic bottle manufacturing industry and plays a crucial role in producing a wide range of consumer products, including water bottles, soda bottles, food containers, and more.​
Mirage Hot Filling Machine
A hot filling machine, also known as a hot filling bottling machine or hot bottling machine, is industrial equipment used in the beverage and food industries to fill containers, such as bottles or jars, with hot liquids or products. This process is commonly used for products that are sensitive to heat, such as juices, sauces, jams, and other viscous or particulate-containing liquids.
​
Hot filling is suitable for products that are acidic or contain natural preservatives, as the elevated temperature helps reduce the risk of microbial growth. The process also helps create a vacuum inside the container after filling, which contributes to sealing and preserving the product.
​
Hot filling machines are utilized in various industries where temperature-sensitive products need to be packaged in containers, ensuring quality, safety, and extended shelf life. The design and features of these machines can vary based on the specific product requirements and the scale of production.


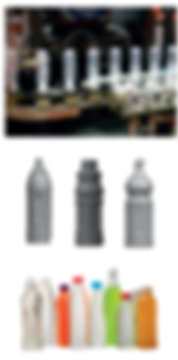
Semi-Automatic Blower



A semi-automatic blowing machine, often referred to as a semi-automatic PET blowing machine, is industrial equipment used in the manufacturing of PET (Polyethylene Terephthalate) plastic containers, such as bottles and jars. It's a type of blow molding machine that falls between fully manual and fully automatic systems in terms of operation and automation level.
​
Semi-automatic blowing machines require some manual intervention for preform loading, mold changes, and container ejection. While they offer a higher level of control and flexibility compared to fully automatic machines, they are generally less automated and have a lower production capacity. They are suitable for smaller-scale production or when production requirements do not demand high-volume output.
​
These machines are commonly used in small to medium-sized manufacturing facilities, particularly in industries that require flexibility in container design and production. As technology advances, semi-automatic blowing machines are being equipped with more automated features, improving efficiency while maintaining a degree of operator involvement.
