Packaging Equipment
After bottles are filled, capped, and labeled, they are often grouped into packs or cases for shipping. Packaging equipment are designed to increase efficiency, reduce human error, maintain product quality, and ensure that bottled products are properly sealed, labeled, and ready for distribution. The specific equipment used can vary depending on the type of beverage, production volume, and packaging requirements.
Shrink Wrapping
Shrink wrapping equipment is a type of packaging machinery used to wrap products in a plastic film that shrinks tightly around them when heated. This process creates a protective and secure package for individual items, bundles of products, or entire cases. Shrink wrapping is commonly used in various industries to package a wide range of products, from consumer goods to industrial items. The plastic film used in shrink wrapping is typically made from materials such as polyethylene or polyolefin.
​
Shrink wrapping offers several benefits, including protection from dust, moisture, and tampering, as well as improved aesthetics and branding opportunities through printed film. It's widely used in retail packaging, food packaging, industrial packaging, and more. The choice of shrink-wrapping equipment depends on factors such as the size and shape of the products, production volume, and the desired level of automation. Talk with our team to learn more about what is best for your production line.
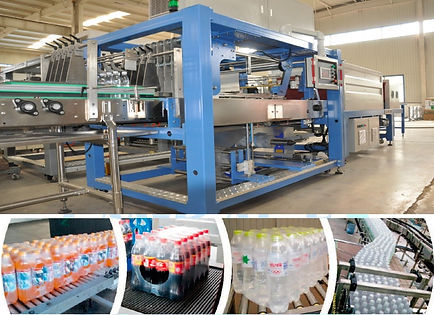

Palletizer Machines
A palletizer machine is an industrial automation tool used to efficiently and accurately stack products, containers, or items onto pallets. This equipment is commonly employed in manufacturing, distribution centers, warehouses, and other facilities that deal with large volumes of goods that need to be organized for shipping or storage. Palletizer machines help streamline the process, improve efficiency, and reduce the need for manual labor in palletizing operations.
​
Palletizer machines offer various benefits, including increased speed, improved stacking accuracy, reduced labor costs, and enhanced workplace safety. They can handle a wide range of products, from bags and boxes to containers and other packaged items. The choice of palletizer machine depends on factors like the type of products being handled, production volume, available space, and specific stacking requirements.
​
Chat with our team today to learn more!





Carton Packaging
Carton packaging refers to the use of cardboard or paper-based materials to create boxes or containers for packaging and protecting products. Carton packaging is widely used across various industries for its versatility, sustainability, and ability to provide branding and information to consumers. It's commonly used for packaging products such as consumer goods, food items, electronics, pharmaceuticals, and more.
​
Carton packaging can be customized to meet the specific needs of different products and industries. It's an essential part of the overall packaging industry, offering both functional and aesthetic benefits to manufacturers and consumers alike.

Gantry Palletizer
A gantry palletizer is a type of industrial machine used for automating the process of stacking products or containers onto pallets. It's commonly used in manufacturing, warehousing, and distribution facilities to efficiently organize and prepare products for shipping and storage. The term "gantry" refers to the structure of the machine, which typically consists of a horizontal beam supported by vertical columns, resembling a bridge or portal.
​
The gantry palletizer operates by lifting products from a conveyor or other source and placing them in precise configurations on pallets. Gantry palletizers offer several advantages, including increased efficiency, reduced labor costs, improved stacking consistency, and reduced risk of injuries associated with manual palletizing. They are suitable for a wide range of products, and their flexibility allows for customization of stacking patterns and configurations.
​
These machines are commonly used in industries such as food and beverage, consumer goods, manufacturing, and logistics, where palletizing large quantities of products is a routine part of the production and distribution process. The gantry design provides a stable and versatile structure that can be adapted to various stacking requirements.

Depalletizer Machine
A depalletizer is a piece of industrial equipment used to automate the process of unloading or destacking items from pallets. This machine is commonly used in various industries, particularly in manufacturing, distribution centers, warehouses, and packaging facilities. The primary purpose of a depalletizer is to efficiently and safely remove products or containers from pallets, making them ready for further processing, packaging, or distribution.
​
​The benefits of using a depalletizer machine include increased efficiency, reduced labor costs, improved workplace safety, and consistent product handling. Depalletizers are particularly useful for high-volume production environments where manual unloading would be time-consuming and labor-intensive. They play a crucial role in streamlining production processes and ensuring that products are ready for downstream operations.
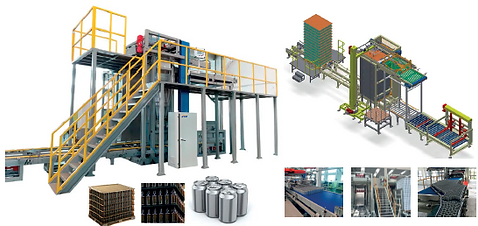
Box Tippers
A box tipper, also known as a bin tipper or container dumper, is a mechanical device used in various industries, including bottling, to efficiently and safely transfer the contents of bulk containers, such as bins or boxes, into a downstream processing line. In the context of bottling production, a box tipper is specifically designed to unload the contents of bulk containers, often filled with raw materials or ingredients, into the bottling or processing equipment. This process helps facilitate the production of beverages, foods, or other products.
​
A box tipper is a specialized piece of equipment that plays a vital role in the bottling production process by automating the unloading of bulk containers and ensuring a steady supply of ingredients or components to the downstream bottling equipment. This automation contributes to increased efficiency, reduced manual labor, and improved overall safety in the production environment.
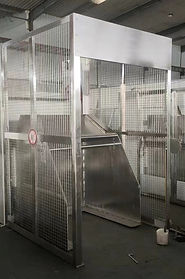

